As relays are the most commonly used control components in non-standard automation control, it is important to understand relay contact materials and life expectancy. Selecting relays with ideal contact materials and longer life expectancy can reduce maintenance costs and lower equipment failure rates.
General purpose and power relays typically have an electrical life expectancy of at least 100,000 operations, while mechanical life expectancy may be 100,000, 1,000,000 or even 2.5 billion operations. The reason electrical life is so low compared to mechanical life is that contact life is application dependent. Electrical ratings apply to contacts that switch their rated loads, and when a set of contacts switches a load smaller than the rating, the contact life may be significantly longer. For example, 240A, 80V AC, 25% P.F. contacts may switch a 5A load for over 100,000 operations. However, if these contacts are used for switching (e.g.: 120A, 120VAC resistive loads), the life may exceed one million operations. The electrical life rating also takes into account arc damage to the contacts, and by using proper arc suppression, contact life can be extended.
Contact life ends when contacts stick or weld, or when one or both contacts lose excessive material and good electrical contact cannot be achieved, as a result of cumulative material transfer during continuous switching operations and material loss due to spattering.
Relay contacts are available in a wide range of metals and alloys, sizes and styles, and the selection of contacts needs to take into account the material, rating and style in order to meet the requirements of a particular application as precisely as possible. Failure to do so may result in contact problems or even early contact failure.
Depending on the application, contacts can be made with alloys such as palladium, platinum, gold, silver, silver-nickel, and tungsten. Mainly silver alloy compounds, silver cadmium oxide (AgCdO) and silver tin oxide (AgSnO), and silver indium tin oxide (AgInSnO) are widely used in general purpose and power relays for medium to high current switching.
Silver Cadmium Oxide (AgCdO) has become very popular due to its excellent erosion and solder resistance as well as very high electrical and thermal conductivity.AgCdO is produced by mixing silver and cadmium oxide using powder metallurgy techniques, and is a material that has electrical conductivity and contact resistance close to that of silver (using slightly higher contact pressures), but due to the inherent solder resistance and arc quenching properties of cadmium oxide, has excellent erosion and welding resistance.
Typical AgCdO contact materials contain 10 to 15% cadmium oxide, and adhesion or solder resistance improves with increasing cadmium oxide content; however, due to reduced ductility, electrical conductivity decreases, and cold working characteristics decline.
Silver cadmium oxide contacts have post-oxidation or pre-oxidation of two kinds, pre-oxidation of the material in the formation of the contact point has been internally oxidized, and than the oxidation of the post-oxidation contains a more uniform distribution of cadmium oxide, the latter tends to make the cadmium oxide closer to the contact surface. Post-oxidized contacts may cause surface cracking problems if the contact shape must be significantly altered after oxidation, e.g., double-ended, moving blades, C-type contact rivets.
Silver Indium Tin Oxide (AgInSnO) as well as Silver Tin Oxide (AgSnO) have become good alternatives to AgCdO contacts, and the use of cadmium in contacts and batteries is restricted in many parts of the world. Therefore, tin oxide contacts (12%), which are about 15% harder than AgCdO, are a good choice. In addition, silver-indium-tin oxide contacts are suitable for high surge loads, e.g., tungsten lamps, where the steady state current is low. Although more resistant to soldering, AgInSn and AgSn contacts have higher volume resistance (lower conductivity) than Ag and AgCdO contacts. Due to their solder resistance, the above contacts are very popular in the automotive industry, where 12VDC inductive loads tend to cause material transfer in these applications.
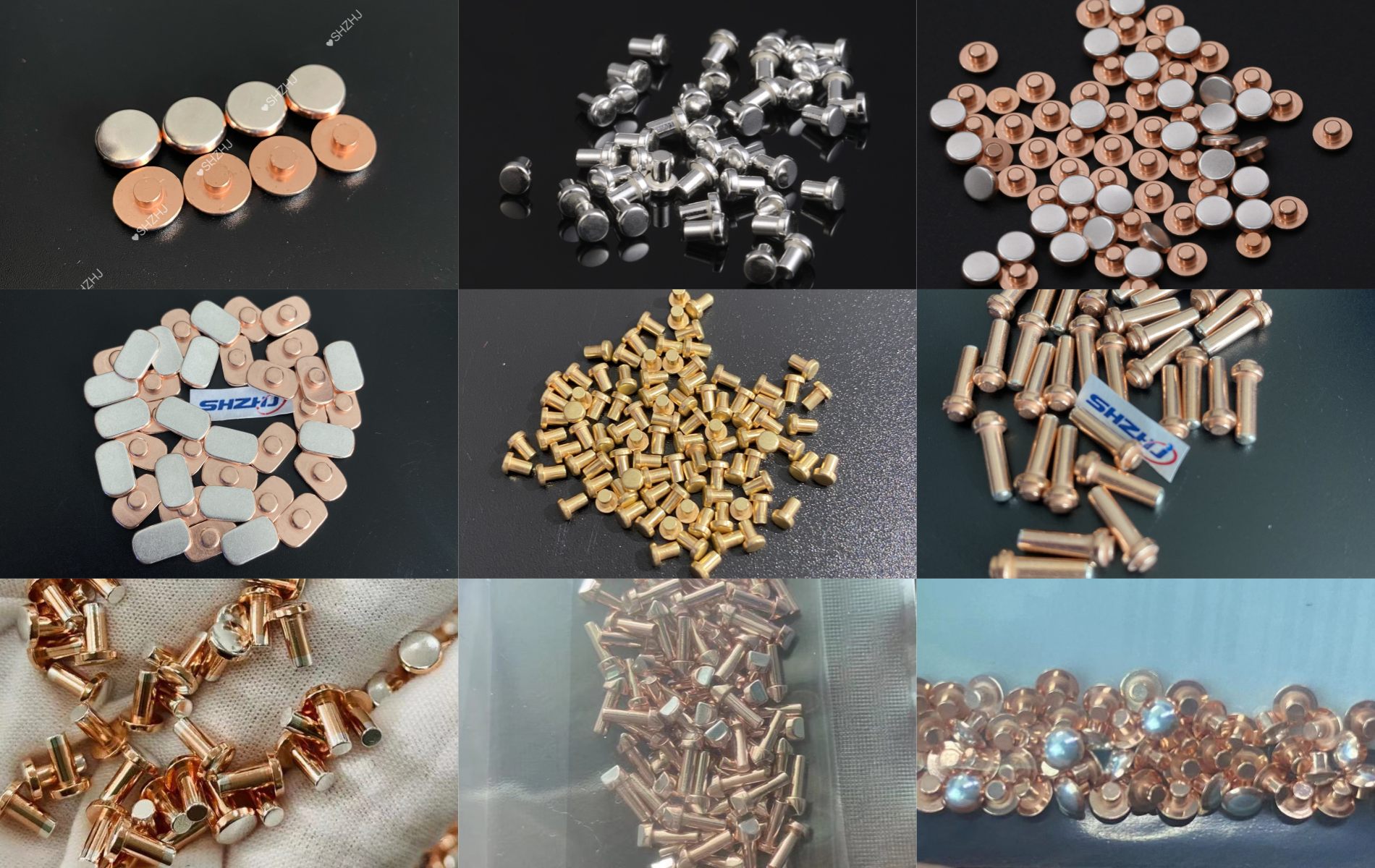
Post time: Apr-01-2024